长期以来,工业产品的设计是基于已有工艺来定型的。由于工艺的限制,在加工和安装方面有不可突破的障碍,使得当前的产品必须由大量的零部件装配而成。这种装配形态,对产品的性能、可靠性、重量、体积、载重、材料、动力、成本、能耗、环保等方面都具有负面影响。
苏氏集成精密成型技术是目前国内外技术水平最先进的精密铸造工艺,实现了“无论产品结构怎样复杂皆可制造”。苏氏精密铸造技术彻底解放了因制造工艺的限制而对产品设计带来的制约,使得在产品研发设计过程中,工程师只需关注产品功能的最佳实现而无需顾忌后续的制造工艺约束,能最大限度地发挥创新性设计的潜能。
突破性的工艺创新,结合工程仿真技术,可以打通产品设计与生产的藩篱,建立设计与制造一体化的工业产品设计体系,让设计突破工艺局限,敢于跨量级优化,产生颠覆式创新。安世亚太和苏氏集团正在利用自身的技术优势,合作打造中国工业再设计体系,并且已经取得一定成果。从已经完成再设计的大量产品来看,工业再设计会使工业品更轻薄、更省钱、更可靠、更美观、更绿色。
更轻薄的设计
降低产品重量对提升操控性,降低成本和能耗等大有裨益。通过再设计,普遍可以实现装备质量15%~60%的减重。
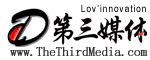
【典型设计】某车桥前桥壳体,通过再设计,实现了将原来由数十个钢制零件焊接而成的前桥壳整体铸造成一个零件,重量下降了50%,且性能不降反升。而且整体铸造的车桥有精确的近净形尺寸精度与形位公差,减少了后续的机械加工甚至免加工,可实现使用过程中的高效率替换和维修。
更省钱的设计
优化设计去除“多余质量”,并降低对高性能新特材料的依赖程度,大幅节省材料成本;产品一次成型,大幅度降低制造、装配成本;更轻的重量,节省设备运行动力成本;更少的零部件,减少后期维护成本。
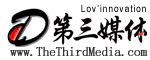
【典型设计】某井下采煤刮板运输机,经过再设计,采用减厚加筋及穿越式结构,一体成型,在不降低性能指标的前提下,每个刮板重量减少33%(13.2Kg),每辆运输机至少200个刮板,能减少2.6吨重量,大幅减少了材料成本和设备动力成本;省略了焊接环节及其他各种连接模式,提高了制造装配的效率和装备的整体可靠性;整体结构有精确的近净形尺寸精度与形位公差,减少了后续的机械加工甚至免加工,可实现使用过程中的高效率替换和维修。
更可靠的设计
突破工艺限制,大胆优化,一体成型,产品结构力学性能与材料力学性能的“最优组合”设计,利用工程仿真技术更精确透视产品特性、加工特性、试验本质以及制造过程,获得最合理的结构、最好的加工方式、高成功率的试验以及最合理的制造装配模式,大幅提高产品的性能和可靠性。
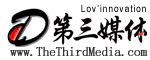
【典型设计】某摩托车车架,通过再设计,整体为一个零件,内部加筋、减小壁厚、减轻重量,改变传统的用焊接铆接方法把多个钢制零件集成为摩托车车架的制造方式,其结构强度、疲劳寿命、可靠性都优于传统的焊接铆接成型车架,避免了焊缝铆接存在所引起的连锁不良效应。更少的零部件,也便于进行仿真分析,仿真结果更加精确。
更美观的设计
无需担心不能制造,可以对当前的产品在结构形貌方面做大胆优化,产生更具创新性的产品。通过材料的重新布局和选择,形成更美观、更复杂的结构,例如12个以上的视角都难以表达的产品。
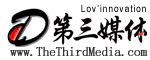
【典型设计】对原结构自行车车架进行优化设计,改变传统用焊接制作模式,整体铸造成型为一个铝质零件,造型自由符合人体工程学,外形更加美观。
更绿色的设计
实施再设计,设计师可以重新设计产品结构的分离面,如无特定必要,产品部件可以设计为一体化结构,无需由大量零件构成。仅此一项改变,对当前产品各方面都会带来直接的改观:性能明显提升、材料可以替换至最低标准、重量下降、载重量提升、保障功能性能的前提下动力要求降到最低、成本下降、能耗、环保指标提升。某些材料(譬如铝材)的焊接工业会造成危害极大的环境污染,对操作人员的身体威胁巨大,减少焊接环节,在绿色环保方面具有不可估量的贡献。
再设计过程产生的是非标准化甚至反传统的产品,没有设计标准及知识经验可参考,唯一能依赖的设计手段就是工程仿真和实物试验。在再设计体系面前,传统的标准、规范、知识和经验都将失效甚至成为创新的制约,所以使得中国工业有机会在某些重点工业产品领域在世界范围内实现弯道超车,为中国工业超越工业强国提供了可能。
(新闻稿 2015-09-28)